Über Kreuz zum Erfolg
Mit dem vorgestellten Ultraschall-Verfahren sind Betreiber in der Lage, Durchflussmessungen durchzuführen. Und zwar ohne dass es dabei zu Kontakt mit dem Medium kommt. Die Methode eignet sich beispielsweise dann, wenn Anwender Medien verwiegen müssen, ohne dabei die Hygiene zu gefährden.
Entscheider-Facts für Betreiber
- Im Hygienebereich arbeiten Betreiber häufig mit Verfahren, bei denen das präzise Dosieren von Ausgangs- und Zwischenstoff entscheidend ist. Für den Prozess als solchen, aber auch für die Wirtschaftlichkeit. Denn die verwendeten Substanzen sind oft hochpreisig.
- Die hierfür erforderlichen Messungen können Betreiber mithilfe verschiedener Methoden durchführen, allerdings sind die häufig mit verschiedenen Nachteilen behaftet. Das nun vorgestellte Messverfahren räumt damit auf.
Flüssigkeiten misst das System ohne Kontakt mit dem Medium oder Produkt per Ultraschallverfahren.
In flüssigkeitsbasierten Herstellungsmethoden hat sie eine zunehmende Bedeutung: die Prozess-Sensorik. Zum Einsatz kommt sie beispielsweise bei der Fermentierung, bei Prozessen mit Mikroorganismen oder bei der Getränkeherstellung- und Mischung. Insbesondere bei zu- und abführenden Flüssigkeitssystemen, die den Durchfluss mittels Pumpen oder Ventilen aktiv oder passiv beeinflussen, spielt eine kontinuierliche Störüberwachung von Schlauchsystemen auf Leerlauf oder Okklusion, die Regelung des geförderten Flusses oder die Erfassung applizierter oder entnommener Flüssigkeitsmengen im häufig aseptischen Produktionsprozess eine wichtige Rolle. Dabei ist das exakte Dosieren der teilweise sehr hochwertigen Ausgangs- oder Zwischenprodukte erforderlich, da diese großen Einfluss auf die Qualität beziehungsweise das Einhalten einer gleichbleibenden Produktformulierung haben. Auch ist eine prozesssichere wirtschaftliche Herstellungsweise ein nicht unwesentlicher Aspekt.
Dokumentierte Qualität
Mit der für die speziellen Anwendungsbedingungen geeigneten Fluss-Sensorik kann eine automatische Prozesskontrolle durch die Ansteuerung von Pumpen oder Ventilen den Durchfluss genau steuern oder regeln. Kritische Prozessschritte lassen sich somit exakt überwachen und rückführbar dokumentieren – wodurch sich Betreiber langfristig Wettbewerbsvorteile sichern können.
Hinzu kommt die Einhaltung der Anforderungen der „guten Herstellungspraxis" (Good Manufacturing Practice, GMP/cGMP), die in vielen Bereichen der Lebensmittel- und Pharmaproduktion Pflicht ist.
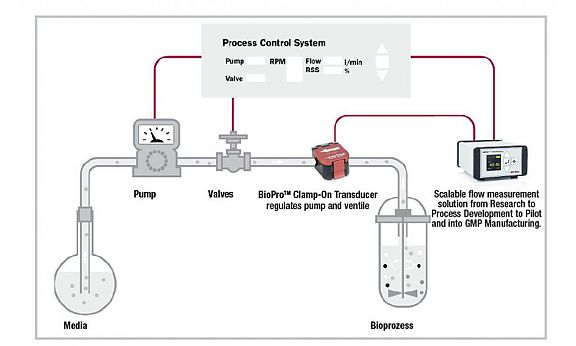
Das Messen von Durchflüssen ist an unterschiedlichen Stellen im Prozessablauf notwendig, sei es beim Vorbereiten oder Anmischen der Rezepturen mit Rohmaterialien, Pufferlösungen oder in anschließenden Veredelungsschritten, beispielsweise der Aufkonzentration von Medien über Membranfilter oder bei Chromatographieanwendungen. Flüssigkeiten werden hierbei sowohl durch Rohre als auch durch unterschiedlichste flexible Schlauchtypen geleitet. Besonders in Prozessen mit hohen Anforderungen bezüglich der Hygiene und Sterilität ist beispielsweise das Reinigen von Edelstahlrohren sehr aufwendig und damit teuer, um die notwendige Reinheit zu erreichen. Oftmals kommen dann – wenn möglich – flexible Schlauchsysteme für den einmaligen Gebrauch zum Einsatz, da die strengen Anforderungen somit einfacher und mit geringerem Zeit- und Kostenaufwand für den Anwender zu erfüllen sind. Im Pharmabereich kommen bei Single-use-Systemen praktisch nur flexible Schläuche zum Einsatz.
Das Verfahren ermöglicht zuverlässige Flussmessung.
Ansprüche an die Durchflussmessung
Um einen Volumenstrom von Flüssigkeiten zu messen, gibt es eine ganze Reihe unterschiedlicher Verfahren, die mehr oder weniger für den Einsatz in der Lebensmittel- und Pharmaindustrie geeignet sind. Da sehr hohe Anforderungen an die Durchflussmessung bestehen, sollte diese präzise sein, einen hohen Messbereich bei hoher Auflösung haben und möglichst wenig in den eigentlichen Prozess eingreifen. Idealerweise erfolgt diese also beispielsweise ohne Medienkontakt und ohne eine Erhöhung von Totvolumina. Sofern Pumpen zum Einsatz kommen, können Anwender den Volumenstrom grundsätzlich einfach, aber indirekt auf Basis der Drehzahl oder der erforderlichen elektrischen Energie einstellen. Der Einsatz zusätzlicher Messmittel ist hier nicht erforderlich. Da dies jedoch bei den häufig verwendeten Rollerpumpen praktisch nur mit einer relativ hohen Ungenauigkeit möglich ist, erfordert es eine permanente Nachkalibrierung, da diese den Schlauch ungleichmäßig auswalken. Auch gibt es bei Zentrifugalpumpen eine Gegendruckabhängigkeit des erzeugten Flusses, der anhand der Pumpenlast nicht richtig abzuschätzen ist.
Bisherige Messmethoden
Eine weitere indirekte Möglichkeit Flussraten zu ermitteln, stellt der Einsatz von Waagen an Behältnissen dar, sofern die Dichte bekannt ist. Waagen sind generell sehr präzise Messinstrumente, allerdings gibt es auch hier eine Reihe von Nachteilen. Zum einen lässt sich nur die Gewichtsveränderung eines kompletten Behälters oder Reaktorgefäßes bestimmen, das heißt parallel zugeführte Medien lassen sich in der Regel nicht ohne weitere ermitteln; außer diese würden immer zeitlich nacheinander zugesetzt. Weiterhin muss die Dynamik des Messbereichs der Waage für das Gesamtgewicht des Behälters inklusive der angebauten Zusetzelemente, wie möglicherweise Rührer, Halterungen für weitere kleiner Behälter etc. ausgelegt sein, was auf Kosten der Auflösung geht.
Das Kalibrieren der mechanischen Waagen ist regelmäßig zu prüfen und mechanisch ungünstige Aufbauten und Umgebungsbedingungen können das Messergebnis beeinflussen, und schränken die Integration ein. Gerade bei großen Behältern in die Unternehmen beispielsweise umpumpen, fällt auch der Raumbedarf der Waagenmechanik entsprechend groß aus.